Lumax Cornaglia Auto Technologies Private Limited expanded their manufacturing facility and they invited us to have a look at what goes on inside
Story: Charan Karthik
Lumax Auto Technologies Limited. The name rings a bell, does it not? Yes, one of the leading manufacturers of lighting components in automobiles. Lumax Auto Technologies Ltd (LATL) entered into a 50:50 joint venture with Cornaglia s.p.a., Italy, in 2007 to form Lumax Cornaglia Auto Technologies (LCAT) and they recently expanded their manufacturing facility at Chakan, near Pune. The new facility is spread over an area of 2.5 lakh square feet and it also houses a 7,000-square foot research and development laboratory.
The facility is equipped with modern machines for manufacturing air filtration systems, snorkels, and various blow-moulded products such as AdBlue tanks and degassing tanks. They have also ventured into and undertaken the production of plastic fuel-tanks for commercial vehicles. LCAT have entered the rotational moulding segment with machines for manufacturing plastic fuel-tanks, fenders, roofs, and mud-guards.
As we entered the premises, we were welcomed by Vikas Marwah, CEO, and department heads who accompanied him to explain what we would be doing today while answering a few of our questions. After introductions, we were joined by Pier Antonio Cornaglia, Director, LCAT, on call where he explained how the company was formed and the journey planned in the future. Cornaglia was founded in 1916 and they started with metal stamping and slowly proceeded towards exhaust systems for automobiles. The Torino-based company is currently valued at €340 million (Rs 3,050 crore) and has over 1,500 employees. Of the three research and development centres, the second biggest one is in India with Lumax as their partner while their biggest is in Torino.
At present LCAT cater to several customers, including Tata Motors, Škoda Auto Volkswagen India, Toyota India and Indonesia, Mahindra, Stellantis, and MG Motor India. LCAT is a key player with their new plant now equipped with a comprehensive range of plastic moulding technologies, as mentioned earlier, that include injection moulding, 2D and 3D blow moulding, and rotational moulding (roto-moulding), a simple but effective technology that enables a variety of customization while producing unique parts in low volumes.
First, we were taken on a short tour around their research and development facility where we witnessed air intake systems for cars being tested. Involving a handful of processes for testing pressure, leakage, and durability, to name a few, we saw how the conventional air duct was different from the dirty side air duct produced with porous material. The latter was lighter in weight, smaller in terms of footprint, and produced a toned down noise while the air was channelled through it, all that will benefit the vehicle’s performance. They have also come up with a rather innovative way of producing an air intake module that suits both the petrol-and a diesel-powered car of a certain manufacturer.
Moving round the spacious factory premises, we were shown around all the processes, getting to know how injection moulding, blow moulding, and rotational moulding were done and we also got to witness first-hand how all of these work. In layman’s terms, the 3D blow moulding machine has a hot piece of plastic blob being dropped by an automated machine into a 3D chamber of specific dimension, which then compresses and blows the blob into the required shape, which, in turn after a few seconds, gives out a small object via a conveyor belt. That is the simple process in which air intakes are manufactured. Later, the excess material that juts out from the sides is carefully examined and cut off for a smooth finish. Multiple quality checks later, the parts are packed and shipped to the original equipment manufacturers (OEM) or manufacturers who require them.
In the production of fuel and urea tanks (AdBlue), LCAT have also come up with a way whereby they combine both the tanks into one with just a partition in between. This saves weight, space, and requires lesser materials for production. It is important for such innovations to come into vogue as they will have a positive impact on the automotive sector in all aspects, from manufacturing to actual use.
After feasting our eyes on these gigantic machines, we were at the end of the production line where air-filters were being made. Thin files of the filter were being arranged in order and put into the plastic housing that forms the perimeter of the filter. The completed product was then segregated and put into boxes which were ready to be shipped off to the customers.
In a different building in the same facility was the roto-moulding machine. It was so huge in size that it re-defined our perception about machines. Climbing up to the machine’s starter/control panel took a few steps and it looked like the time travel machine from the film Avenger’s Endgame. The Reinhardt machine is capable of producing eight fuel-tanks in 23 minutes, a process that is both quick and facilitates a lot of customization.
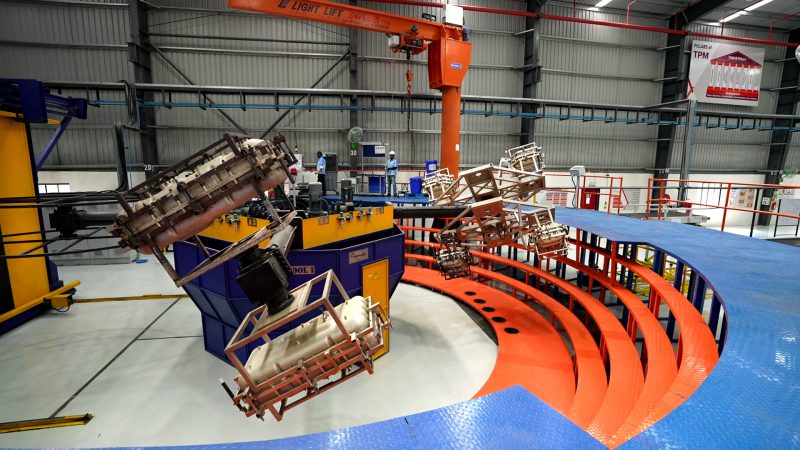
The cool-looking rotational moulding machine
In a quick conversation with Vikas Marwah, he described how the entire process for the dirty side air duct starting from development to mass production, with everything in between considered, took them nearly 24 months. We also asked him if the company only produces said parts (air intakes) for engines manufactured in our country or also for engines that have been exported from other countries. He said that it depended on what the customer (OEM) required and what they could offer to them from their capability. The cost of setting up a roto-moulding machine in India is nearly Rs 10 crore, he mentioned, adding that only a handful of manufacturers have this set-up.
- Pier Antonio Cornaglia, Director, LCAT
- Vikas Marwah, CEO, LATL
The Lumax Cornaglia Auto Technologies factory visit proved to be insightful and, as the title suggests, offered us an edifying look at what goes on behind the shutter.